Source: PV Magazine
The time for BESS is now
With its battery storage solutions that allow powering household loads with or without the grid, Growatt has deepened its market presence in the United States in recent years and set up local service centers. To meet different customer needs, the manufacturer offers two different solutions – Whole Home and Partial Home Backup. With flexible capacity options starting from 6.6 kWh and up to a maximum of 39.6 kWh of energy output, Growatt provides its 311.4 kW MIN XH-US residential hybrid energy storage system, with an option to enable whole-home backup both in peak time and blackout.
Clearly, power outages are not solely limited to the United States. Down Under, Australians have endured a number of extreme weather events and bushfires over recent years. Many times, such climate crisis-induced events have left thousands of homes without power for extended periods. On top of that, eco-conscious Australians, who are already leading the world in residential PV installs – with nearly 1 kW of PV installed per person, according to the data from the Australian PV Institute – continue to demonstrate the desire to further reduce the carbon footprint of their own homes.
Australian installed
30,246
residential batteries in 2021
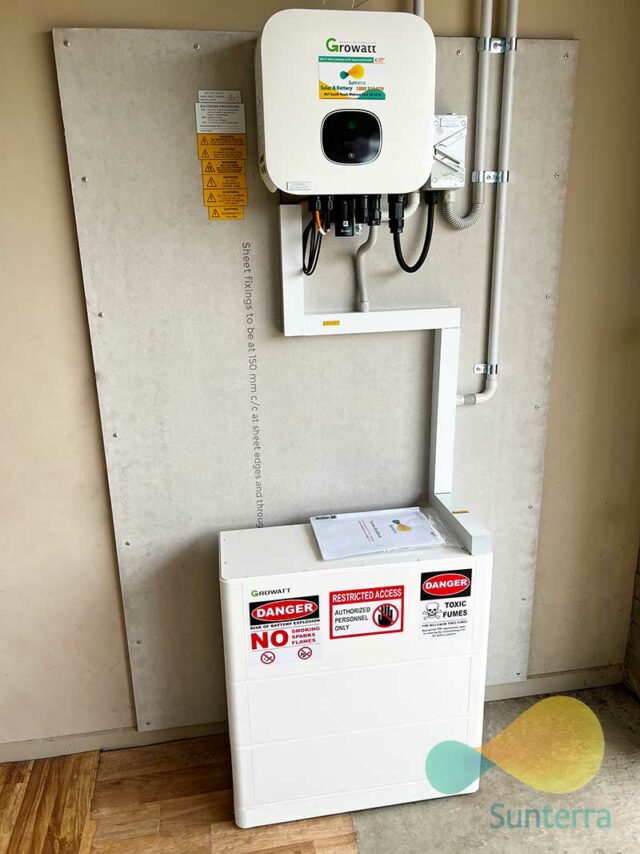
State government incentives are playing a major role in driving BESS uptake in Australia. In 2020, the South Australian government had to reduce its subsidy to avoid overheating the market and in Victoria, the popularity of home batteries was so high the state government subsidy allocations were exhausted within minutes of each release.
According to the local solar and storage market analyst SunWiz, the residential battery market remained steady in 2021 with 30,246 systems installed. Australia is expected to continue its shift to batteries with one pronounced trend – customers’ growing preference for top-notch products.
With its local subsidiary in Australia established back in 2011, Growatt has emerged as a top brand for residential PV and energy storage markets. “According to our experience in Australia, customers’ preferences always focus on high quality, whole system solutions to prevent maintenance issues, and higher DC overloading to harvest more energy,” says Cheng
In some regions, more than 50% of new solar installations now come with a battery. Many customers with older solar arrays are now looking to retrofit energy storage to maximize their self-consumption.
“Australia is expected to continue its shift to batteries with one pronounced trend – customers’ growing preference for top-notch products”
Five steps to ensure battery quality
Rigorous process control is of utmost importance in lithium-ion battery manufacturing – thermal runaway can lead to catastrophic failures, including fires. For Growatt, there is no room for compromise when it comes to quality in battery manufacturing. Growatt’s ARK was recognized as “outstanding” in TÜV Rheinland’s stringent safety and reliability tests. It also won the prestigious All Quality Matters Award.
Here are five steps by which Growatt has achieved this success.
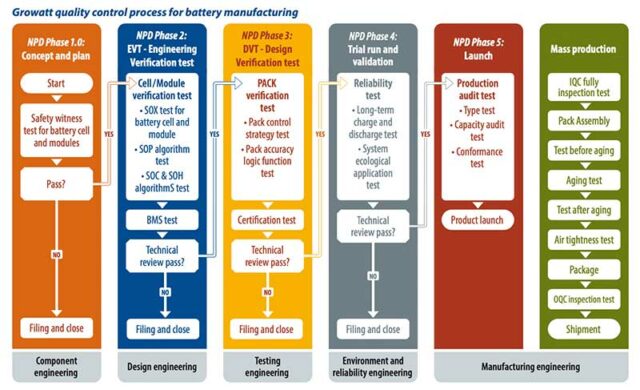
High quality never happens by chance. It is always the result of comprehensive, well thought out, and concerted effort. For Growatt, quality is the lifeline spanning the company’s entire spectrum of operations and extensive portfolio of products, including PV inverters, energy storage systems, EV chargers, and smart energy management solutions.
The Shenzhen-based manufacturer first promoted its storage products back in 2015 and has since expanded its port- folio to include a variety of DC- and AC- coupled solutions for residential and small commercial use. At the end of 2021, Growatt had delivered around 3.8 million sets of its PV inverter and battery systems.
Cutting-edge production
Growatt’s battery manufacturing is co- located with its PV inverter production in Huizhou, China. Spread over approximately 200,000 square meters, its manufacturing facility has an annual capacity of 20 GW of PV inverters and 400,000 battery modules. Faithful to the lithium iron phosphate (LFP) chemistry because of its extreme safety, Growatt has released multiple models of its branded battery energy storage systems, such as AXE, Hope, GBLI and the ARK series.
All of Growatt’s battery systems have gained a good reputation in the market thanks to high quality and reliability, not to mention confirmation by independent testing service providers. Last year, Growatt’s modular ARK residential battery energy storage solution achieved outstanding performance in TÜV Rheinland’s rigorous safety and reliability tests and won the prestigious All Quality Matters Award. As might be expected, for Growatt, quality is all that matters.
“Growatt would never compromise on quality, even under the cost pressure,” says Ray Cheng, head of overseas marketing at Growatt. “We’re very certain the high quality of products can bring cost savings for the company in different ways, such as through reducing maintenance cost or saving marketing costs that occur due to any quality defects.”
Step by step
To deliver top-notch reliability and per- formance, Growatt strictly executes its tested Five Step Quality System for the new product development and mass pro- duction process. The first step of the sys- tematic quality program is Component Engineering. At this stage, Growatt con- ducts safety tests for the battery cell and module, including over-charge, over-dis- charge, short circuit, dropping test, ther- mal runaway test, extrusion test, seawa- ter immersion test, temperature changing test, low air-pressure test, and the shaking test with the goal to ensure that fire, explo- sion, or leakage accidents do not happen under the worst conditions.
For instance, in the thermal runaway testing, a heating element is placed near a battery cell exposing it to temperatures up to 215 C. As soon as the heat is spread to the adjacent battery cell, an explosion- proof valve will open, preventing fire.
For the second step, Design Engineer- ing, Growatt conducts a variety of engi- neering verification tests, including state- of-charge (SoC) and state-of-health (SoH), to verify the charge and discharge accuracy under different C rates and tem- peratures, alongside charge/discharge switch tests. In addition, the battery man- agement system (BMS) test and the state of power (SOP) algorithm import test are also critical for the battery.
The BMS is the brain of the system and the first in line to provide full protection in cases of over/under temperature, over/ under voltage, over current, and short circuiting. One of the critical parts of the BMS test is real-time data collection, cov- ering temperature, SoC, cell and pack voltage, charge and discharge current sampling and other parameters, giving a comprehensive picture of the battery’s sta- tus and health at any given moment.
Next comes the design verification test stage, in this Growatt assembles the energy storage system and combines inverters, batteries, and monitoring devices to verify that all the elements work seamlessly as a whole under various external conditions.
For the fourth step, Environment and Reliability Engineering in the trial-run
and validation stage, Growatt conducts long-term charge and discharge cycle tests and capacity and conformance tests to assess battery status in the full life cycle. In addition, it runs the ecological applica- tion tests to guarantee that the whole sys- tem is operating reliably in different appli- cation scenarios.
The Manufacturing Engineering stage focuses on both product launch and mass production. In the product launch stage, the manufacturer conducts product audit tests, such as the type test, capacity audit test, and conformance test. Overall, there will be at least 128 testing steps for the bat- tery product development, ensuring an exhaustive and extensive quality assur- ance process.
On top of the rigorous in-house regime, all battery storage products made by Growatt are also subject to the third-party verification tests to achieve global certifications such as CE, IEC 62619, VDE 2510, UL1973, UL9549, UN38.3 MSDS, and more. Finally, for the mass production stage, Growatt cutting- edge manufacturing facility has achieved quality management system certificates ISO 9001, ISO14001 and ISO 45001. In addition, the manufacturer conducts full tests for the whole manufacturing pro- cess, including IQC inspection, module test, aging test, air tightness test, and package test to deliver superior quality products and excellent customer expe- rience.
For battery products, Growatt’s quality assurance process involves at least
128
separate testing steps
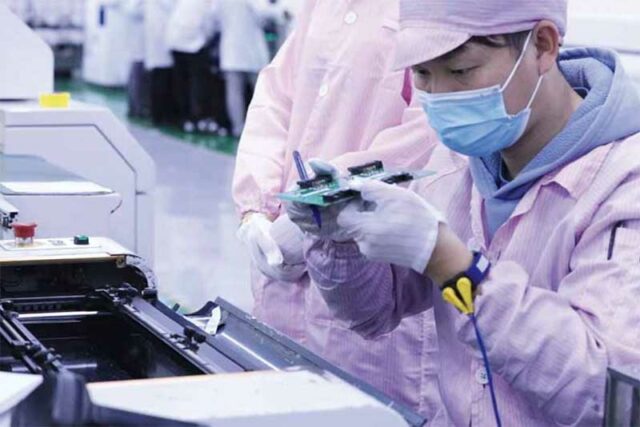